CoroMill® MH20 de la Sandvik Coromant optimizat pentru caracteristici ale componentelor cu lungimi mari în consolă.
Inginerii care prelucrează componente utilizate în industria aerospaţială nu îşi pot permite să facă greşeli. Standardele de control al calităţii pentru aceste componente sunt incredibil de ridicate, contând cu atât mai mult la utilizarea sculelor lungi pentru a prelucra găuri înfundate şi înguste. Aici, Sangram Dash, Manager în aplicarea produselor pentru freze amovibile în cadrul Sandvik Coromant, explică modul în care freza cu avans mare CoroMill® MH20 poate asigura producţia fără erori în prelucrarea componentelor utilizate în industria aerospaţială.
Prelucrarea componentelor pentru industria aerospaţială este o provocare. Producătorii produc componente cu podele şi pereţi subţiri, găuri înfundate şi colţuri înguste. Aceste caracteristici necesită o sculă care să asigure aşchiere uşoară, să ofere stabilitate ridicată în funcţionare şi să menţină un control stabil ― mai ales la utilizarea sculelor lungi pentru frezarea găurilor înfundate şi înguste.
Capacitatea sculei de prelucrare la lungimi mari în consolă este o cerinţă importantă pentru frezarea găurilor înfundate şi înguste, ceea ce se întâmplă adesea în cazul fabricării componentelor, cum ar fi traversele de susţinere întâlnite în subsectoarele industriei aerospaţiale. Aceste traverse sunt adesea prelucrate din titan forjat şi, atunci când sunt asociate cu cerinţe pentru lungimi mari în consolă, creează un mediu dificil de prelucrare, cu un risc ridicat de apariţie a vibraţiilor.
Vibraţiile produse în timpul prelucrării pot duce la imperfecţiuni superficiale ale piesei de prelucrat, ceea ce afectează calitatea produsului final. Alte probleme legate de vibraţii includ faptul că grosimea aşchiilor nu rămâne constantă şi, din această cauză, variază şi forţele de aşchiere. În unele cazuri, vibraţiile pot cauza ruperea plăcuţei sau a sculei.
Mai puţine colţuri
Ca răspuns la această provocare, Sandvik Coromant a dezvoltat CoroMill® MH20, o nouă freză cu avans mare concepută în principal pentru frezarea cavităţilor sau a găurilor, în materiale ISO S, M şi P.
Designul frezei CoroMill® MH20 prezintă mai multe inovaţii, inclusiv un nou material pentru corpul frezei, care a fost folosit pentru corpurile cozilor cilindrice pentru a minimiza uzura în timpul prelucrării. Materialul reduce frecarea şi formarea aşchiilor, care are loc atunci când tensiunile mari sau forţele de aşchiere creează deformări plastice pe locaşul plăcuţei. Funcţiile frezei CoroMill® MH20 vor asigura o durabilitate optimizată a sculei.
În momentul proiectării sculei, inginerii Sandvik Coromant au ţinut cont de cerinţele stricte ale industriei aerospaţiale. De exemplu, scula este capabilă să finalizeze mai multe operaţii cu caracteristici diferite, reducând numărul de scule utilizate, numărul de schimbări ale sculelor şi gradul de manevrare a sculelor necesare în timpul producţiei. Acest lucru ajută la reducerea timpilor de ciclu şi îmbunătăţeşte aspectul economic al procesului de producţie.

În plus, pentru prima dată în conceptele de scule cu avans mare, Sandvik Coromant a introdus geometrii de plăcuţe dedicate pentru domenii de certificare ISO diferite, pentru o mai bună securitate şi productivitate a procesului. În contrast cu conceptul convenţional de freze cu plăcuţă cu patru muchii, freza CoroMill® MH20 este prevăzută cu o plăcuţă cu două muchii. Acest lucru este benefic, deoarece înseamnă că cea mai slabă secţiune a plăcuţei este departe de zona principală de aşchiere, asigurând o mai mare fiabilitate şi protecţie împotriva uzurii. De asemenea, presupune faptul că prelucrarea într-un colţ sau pe un perete nu va avea un impact asupra muchiei următoare sau a colţului anterior, garantând o performanţă uniformă per muchie.
Un alt aspect inovator îl reprezintă geometria muchiei aşchietoare a plăcuţei frezei CoroMill® MH20. Designul înclinat al muchiei oferă o acţiune de aşchiere treptată şi uşoară, ceea ce necesită un consum redus de energie pentru a permite utilizarea unor maşini mai mici. Muchia aşchietoare principală optimizată şi raza la vârf a plăcuţei garantează siguranţa sporită a procesului.
Prelucrarea de precizie
Un client fidel al Sandvik Coromant, un subcontractor din industria aerospaţială, se confrunta cu probleme în timpul prelucrării componentelor cu arbori lungi şi subţiri pentru aeronave. Un arbore este o componentă rotativă care se ataşează la elice şi susţine alezajul care vine peste arborele elicei, astfel încât alezajul să asigure rotire liberă şi stabilă. Arborii, care erau o componentă nouă pentru client, s-au dovedit a fi dificil de prelucrat din cauza dimensiunilor lor excentrice şi uneori extreme, fiind imposibil de rotit în unele cazuri.
În consecinţă, găurile frezate în piesa de prelucrat din aliaj Inconel erau uneori descentrate cu doi sau trei milimetrii. În plus, scula existentă a clientului prezenta o durabilitate foarte redusă şi o mulţime de resturi de aşchii care sugerau o conexiune slabă între maşină şi sculă. Componentele arborelui chiar se îndoiau în unele cazuri, deoarece freza împingea componenta în loc să aşchieze materialul.
Ca soluţie a fost identificată roto-frezarea, care presupune rotirea piesei de prelucrat în jurul punctului său central. Această tehnică de frezare este adesea recomandată în cazurile în care formele unui produs deviază considerabil de la cele obţinute prin frezare convenţională ― aşa cum s-a întâmplat în cazul arborilor. Cu toate acestea, când s-a încercat roto-frezarea pentru prima dată, clientul a întâmpinat probleme legate de vibraţii.
Pentru a rezolva aceste probleme, Sandvik Coromant a recomandat freza CoroMill® MH20 pentru operaţia de roto-frezare. Freza a fost aleasă pentru acţiunea sa de aşchiere foarte uşoară, pentru a preveni îndoirea componentei, oferind în acelaşi timp un preţ mai competitiv per muchie. Freza CoroMill® MH20 s-a integrat cu uşurinţă în configuraţia clientului. O altă provocare a fost însă faptul că clientul nu mai folosise niciodată tehnica de roto-frezare. Specialiştii Sandvik Coromant au lucrat îndeaproape cu acesta pentru a-i explica tehnica şi au oferit recomandări şi instrucţiuni pentru programul de frezare cu control numeric computerizat (CNC).
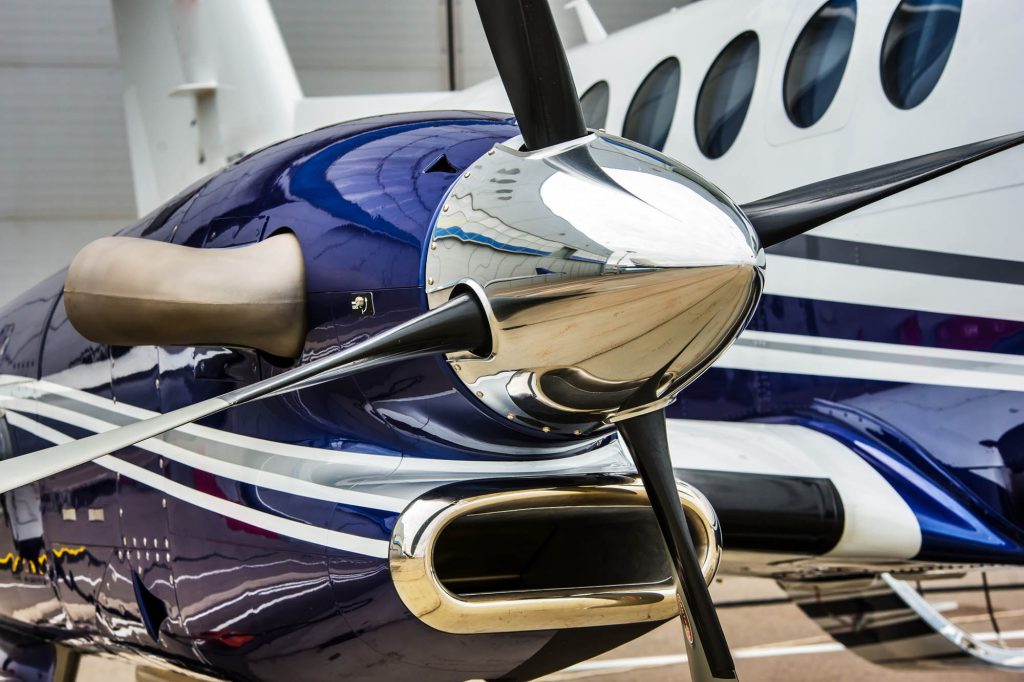
Freza CoroMill® MH20 a fost utilizată pentru a prelucra Inconel 718 şi A286, un aliaj pe bază de fier cu rezistenţă ridicată şi caracteristici excelente de fabricaţie, fiecare dintre aceste materiale fiind populare în industria aerospaţială. Scula a funcţionat la o viteză de aşchiere (vc) de 40 m/min, un avans pe dinte (fz) de 0,3 mm/dinte şi o adâncime de aşchiere axială (ap) de 0,5 mm. În mod esenţial, a fost necesar ca freza CoroMill® MH20 să depăşească performanţele sculei existente a clientului în doar 30 de minute de prelucrare, astfel încât să se evite riscul de apariţie a vibraţiilor.
În cele din urmă, CoroMill® MH20 a demonstrat o durată de viaţă îmbunătăţită. În plus, un mare avantaj al sculei a fost aşchierea foarte uşoară, ceea ce a permis o prelucrare precisă care fusese imposibilă cu scula anterioară şi care a putut fi obţinută cu parametrii de aşchiere optimizaţi şi într-un timp de prelucrare mai scurt de 30 de minute. În cele din urmă, CoroMill® MH20 a realizat acest lucru cu unul sau doi dinţi mai puţin decât scula concurenţei.
Soluţia de aşchiere de la Sandvik Coromant a deschis oportunităţi referitor la prelucrarea buzunarelor pentru subcontractorul din industria aerospaţială. Prin îmbunătăţirea CoroMill® MH20, clientul a obţinut o durabilitate a sculei îmbunătăţită semnificativ şi procese de prelucrare mai sigure şi fără vibraţii. Cu aceste avantaje, scula aşchietoare s-a dovedit utilă la prelucrarea de precizie a materialelor dure, inclusiv la lungimi mari în consolă şi, în special, în raport cu standardele privind controlul calităţii pentru componentele aeronavelor.