Celulele de baterii litiu-ion (LIB) cu costuri reduse reprezintă cheia electromobilității de masă, deși procesul de fabricație a reprezentat întotdeauna un factor de cost – până acum. Cercetătorii de la Universitatea Tehnică din Berlin folosesc plierea continuă în Z pentru a înlocui mișcările tradiționale de preluare și plasare utilizate până acum, accelerând astfel producția de celule de baterii. Sistemul de transport liniar XTS de la Beckhoff a jucat un rol crucial în acest caz.
Cea mai mare provocare în producția de celule de baterii litiu-ion (LIB) este faptul că asamblarea compozitului electrod-separator, care constă din mai multe straturi, este foarte lentă. Pentru structurile pliate în Z destinate vehiculelor electrice sunt necesare multe operații de preluare și plasare efectuate de roboți sau cinematici speciale. Procesul este consumator de timp, deoarece fiecare electrod necesită o operațiune de pick-and-place, iar o singură LIB de 50 Ah are până la 53 de electrozi individuali în format 300 x 125 mm.
“Problema și blocajul de productivitate sunt în mod evident cauzate de aceste numeroase mișcări de preluare și plasare“, explică Dr.-Ing. Arne Glodde, cercetător principal la Institutul de mașini-unelte și management al fabricii (IWF), Departamentul de tehnologie de manipulare și asamblare de la Universitatea Tehnică din Berlin. El spune că timpii de manipulare și de asamblare nu pot fi reduși pur și simplu prin frânarea și accelerarea mai rapidă a roboților industriali. “Acest lucru ar afecta precizia de poziționare la plasarea electrozilor“, afirmă Dr. Arne Glodde. Acest lucru ar duce la un grad mai mic de acoperire în rețeaua de celule, în detrimentul capacității celulelor, a duratei de viață și chiar a scurtcircuitelor. “Fluxul de proces anterior și-a atins limita de productivitate din punct de vedere practic“, subliniază Dr. Arne Glodde, referindu-se la ceea ce a fost, în cele din urmă, impulsul care a dus la dezvoltarea noului proces de producție LIB.
Stivuirea bateriilor accelerată cu 150%
Cercetătorii de la Universitatea Tehnică din Berlin au înlocuit procesul de preluare și plasare cu un transport continuu de material al electrozilor și al separatorului. “Acest lucru ne-a permis să creștem producția cu peste 150% în comparație cu procesul actual de ultimă generație“, spune Dr. Arne Glodde, subliniind cea mai semnificativă îmbunătățire. Această creștere a randamentului înseamnă că, în viitor, vor putea fi produse 250 de celule în timpul necesar pentru a produce 100 în prezent. Inovația cheie în acest proces este tehnica patentată de pliere în Z, bazată pe sistemul de transport liniar XTS și pe dispozitivele sale de prindere rotative. Două dintre aceste sisteme, cu un total de zece dispozitive de deplasare, asigură o pliere continuă cu poziționarea precisă a electrozilor în stivă.
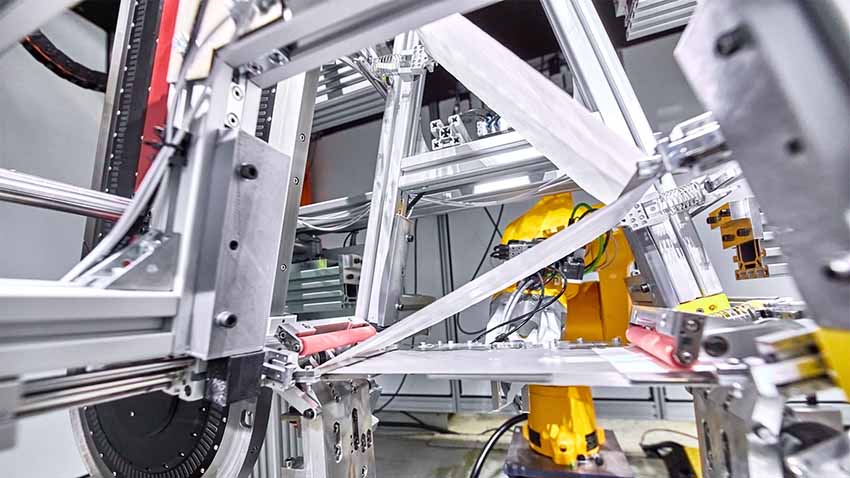
Electrozii sunt disponibili sub formă de stive de foi individuale, iar separatorul este disponibil sub formă de bandă. Utilizând un proces bazat pe vid, electrozii flexibili sunt ridicați fiecare de o rolă individuală și accelerați la viteza benzii separatoare. În timpul transportului, pozițiile sunt detectate, iar foile de electrozi sunt aliniate cu precizie cu separatorul. Electrozii sunt apoi fixați alternativ pe materialul separator în timp ce acesta este transportat continuu.
Aceasta este urmată de plierea în Z, prin care banda de separare cu electrozii fixați pe ea este introdusă în procesul de pliere de sus prin intermediul a două role de ghidare. În acest scop, două role de comutare deviază materialul benzii și facilitează prinderea alternativă din spate cu ajutorul unor dispozitive de prindere speciale. Aceștia sunt montați pe dispozitivele de deplasare ale celor două sisteme XTS interconectate și ghidează pliurile până când materialul de pe bandă este depus pe masa de pliere, unde un sistem de prindere fixează pliurile. Sistemele XTS sunt montate într-o structură fără vibrații care poate fi integrată în secvența individuală a oricărui sistem de producție de baterii.
XTS deschide potențialul pentru inovație
“Fără sistemul de transport liniar de la Beckhoff, nu am fi reușit să implementăm în mod corespunzător plierea continuă în Z cu acest control al procesului și să obținem acești timpi de procesare semnificativ mai mici“, spune Dr. Arne Glodde. Timpul de procesare a fost redus de la peste o secundă pe pliu la 0,7 s pentru compozitele de electrozi-separatori pliați în Z de format mare, iar procesul este încă departe de a atinge limitele potențialului său. În viitor, ar putea fi atinși timpi de aproximativ 0,35 s pe pliu.
Pentru a crea un pliu în 0,7 s, dispozitivele de deplasare se deplasează la o viteză de aproximativ 600 mm/s. Pentru un timp de 0,35 s pe pliu, această viteză ar fi de aproximativ 1.000 mm/s. “XTS-ul nostru este proiectat să se deplaseze cu o viteză standard de până la 4 m/s, deci are suficientă capacitate pentru a accelera și mai mult procesul“, declară Guido Sieder, inginer de vânzări la sucursala Beckhoff Berlin. “Proprietățile mecanice ale materialului separatorului și momentele de inerție vor fi, probabil, întotdeauna factorii limitativi pe termen lung“, confirmă Dr. Arne Glodde.
Caracteristicile speciale ale XTS și controlul pe bază de PC sunt responsabile pentru actualul salt de performanță. Dr. Arne Glodde menționează: “Cu ajutorul mișcărilor sale controlabile în mod liber, XTS dă viață secvenței noastre de mișcare exigente.” Dispozitivele de prindere trebuie să fie deplasate unul în raport cu celălalt pentru a plia materialul cu o tensiune adecvată a curelei, făcând față în același timp solicitărilor. Deși acest lucru poate părea simplu, necesită de fapt o tehnologie de automatizare de înaltă performanță, dar flexibilă:
- TwinCAT trebuie să calculeze cu precizie și în timp real poziția unui dispozitiv de mișcare în raport cu poziția celorlalte dispozitive de mișcare.
- Sincronizarea precisă a rolelor pe o distanță cât mai scurtă necesită o dinamică ridicată.
- Numărul de dispozitive de mișcare care intervin în mod activ trebuie să poată fi ajustat în mod dinamic în timpul procesului.
- Pentru a se asigura că pozițiile de-a lungul benzii separatoare sunt abordate la momentul potrivit, este necesar un grad ridicat de repetabilitate.
- Fluctuațiile de sarcină necesită un control de înaltă calitate.
“Pentru a calcula și a controla toată cinematica în timp real, a trebuit să ne asigurăm că axele servo XTS pot trece fără probleme de la funcționarea NC (punct la punct) la interpolare“, explică Mathias Arndt, inginer de aplicații la sucursala Beckhoff din Berlin. Dr. Arne Glodde, responsabil de proiect, spune că programarea și sincronizarea controllerelor în funcție de module, datorită capacităților multitasking ale TwinCAT, a fost, de asemenea, foarte utilă în timpul implementării.
Planificarea traiectoriei pentru toate axele este realizată direct în controler pe baza calculelor cinematice efectuate. Secvențele din celelalte module sunt cuplate prin intermediul axelor virtuale și corectate prin mișcări de suprapunere în raport cu celelalte elemente din proces. Un alt punct pozitiv pentru Dr. Arne Glodde este integrarea și sincronizarea simplă a cinematicii robotului cu șase axe care ejectează pachetele de electrozi pliate.
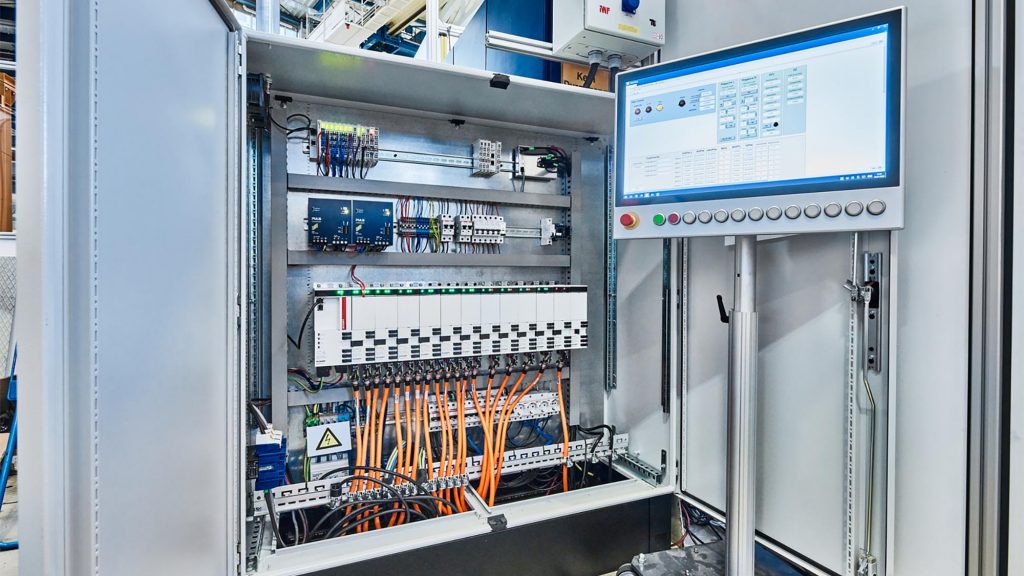
Detectarea poziției obiectelor cât mai rapid și mai exact posibil este crucială pentru precizie și repetabilitate. Cercetătorii din Berlin s-au bazat pe tehnologia XFC pentru a asigura acest lucru. “Utilizăm funcția de înregistrare temporală a tehnologiei eXtreme Fast Control pentru calcularea pozițiilor“, precizează Dr. Arne Glodde, “iar achiziția semnalului devine astfel independentă de ciclul PLC“. Avantajul este că tehnologia de control nu mai este factorul limitativ în detectarea poziției; în schimb, tehnologia actuală a senzorilor cu rate de eșantionare de 62,5 kHz constituie aici limita.
Accelerare suplimentară prin intermediul dispozitivelor de prindere controlate în mod activ
Este de la sine înțeles că Dr. Arne Glodde și echipa sa lucrează la împingerea limitelor pliabilității Z și mai departe. “De fapt, observăm o precizie mai scăzută la viteze mai mari din cauza vibrațiilor și a forțelor inerțiale. Acest lucru ar putea fi contracarat cu șine de ghidare și mai rigide sau cu dispozitive de prindere active.” Beckhoff are soluții pentru ambele: sistemul de transport liniar XTS, cu sistemul său de ghidare în formă de V și tehnologia No Cable Technology (NCT) pentru transmiterea fără fir a comunicațiilor și a energiei electrice către dispozitivele de mișcare, mărește posibilitățile de optimizare suplimentară, făcând procesele de pliere mai rapide și mai flexibile.
“Mai precis, lucrăm la dezvoltarea ulterioară a dispozitivelor noastre de prindere și dorim să folosim NCT pentru a înlocui ghidarea mecanică pozitivă cu un control activ al dispozitivelor de prindere“, spune Dr. Arne Glodde. Acest lucru sporește flexibilitatea sistemului în ceea ce privește formatele de electrozi și permite compensarea dinamică a erorilor de alimentare. “În plus, dorim, de asemenea, să integrăm un sistem de viziune în sistem pentru asigurarea calității“, afirmă Dr. Arne Glodde, prezentând planurile de extindere viitoare.

KREATRON AUTOMATION SRL