Expresia smart factory,”fabrică inteligentă”, a fost inventată pentru prima dată în 2011, în cadrul expoziției comerciale din Germania, Hanover Messe. Termenul descrie un mediu puternic digitalizat în care utilajele se optimizează și funcționează în mod autonom. Cu toate acestea, deși se află în vocabularul nostru de aproape un deceniu, fabricile inteligente nu sunt încă ceva obișnuit. Aș dori să subliniez faptul că “fabricile conectate” ar putea fi primul pas în realizarea digitalizării în producție.
O fabrică conectată descrie o instalație care utilizează tehnologia digitală pentru un schimb de informații fără întreruperi între oameni, mașini și senzori. Spre deosebire de inițiativele privind fabricile inteligente, se pune mai puțin accent pe utilaje și mai mult pe conectivitate.
Inițiativele privind fabricile conectate se pot derula în paralel cu proiectele privind fabricile inteligente. Cu toate acestea, obiectivul fabricii conectate se concentrează în întregime pe automatizarea proceselor mecanice, dar și pe atingerea unei stări ideale de producție prin productivitate durabilă, autocorecție și calitate. Dar, cum se poate atinge această stare?
Primul pas: Puneți datele la dispoziție pentru decizii
Fabricile conectate sunt dezirabile datorită ofertei unice pe care o oferă lucrătorilor și a faptului că le dau posibilitatea de a lua decizii. Luați ca exemplu un inginer de întreținere. Într-o fabrică conectată, inginerul va avea vizibilitate asupra întregii operațiuni a fabricii prin conectivitatea dintre utilaje, senzori și software-ul fabricii.
Utilizând o platformă software cu un tablou de bord adecvat, acesta poate filtra datele unui anumit utilaj și le poate suprapune cu programul de producție al fabricii. Folosind această perspectivă, ei pot decide care este momentul optim pentru a programa întreținerea.
Combinația de control, vizibilitate și flexibilitate a fabricii conectate le permite lucrătorilor să ia decizii mai bune – în contrast pur și simplu cu concepția greșită conform căreia fabricile de producție puternic digitalizate dezavantajează angajații și deplasează locurile de muncă.

Pasul doi: Implementarea și îmbunătățirea
Spre deosebire de investiția statică a unei piese de hardware automatizat, investiția în conectivitate oferă un flux constant de date din care se pot extrage informații. Prin urmare, fabricile conectate oferă producătorilor posibilitatea de a-și îmbunătăți continuu procesele.
În timp ce fabricile inteligente futuriste imaginate pentru prima dată la Hannover Messe din 2011 se concentrau în mare parte pe hardware și automatizare robotică, fabricile conectate care sunt conduse în mare parte de date promit o modalitate mai realizabilă – și adesea mai avantajoasă – pentru producători de a-și digitaliza instalațiile.
Pasul trei: Clarificați comunicațiile
Fabricile conectate oferă, de asemenea, un limbaj comun pentru diferitele părți interesate. Așa cum inginerul de întreținere menționat mai sus va găsi împuternicire prin intermediul datelor privind performanța mașinilor, același lucru este valabil și pentru operatorii de producție, managerii de energie și directorii de nivel c și seturile lor de date.
Spre deosebire de jargonul de afaceri care deseori îngreunează conversațiile între departamente în industrie – gândiți-vă la Industria 4.0, sistemele cibernetice-fizice și discuțiile despre ergonomia industrială – fabricile conectate oferă cunoștințe bazate pe date. Datele sunt obiective și pot fi procesate într-un mod pe înțelesul tuturor.
Pasul patru: Creați obiective interdepartamentale
Atunci când comunicarea este activată prin mai multe programe informatice, aceasta permite diferitelor domenii de activitate să colaboreze și să stabilească obiective mai complexe. Obiectivele pot fi legate de calitate, sustenabilitate, flexibilitate, pierderi și multe altele – asta pe lângă câștigurile evidente de producție ale proiectelor de digitalizare.
Odată ce obiectivele sunt confirmate, este posibil ca fiecare angajat să determine starea ideală a unei instalații în funcție de cerințele sale. De exemplu, dacă inginerul de întreținere plănuiește să atingă zero timp de nefuncționare neplanificat din cauza defectării echipamentelor, el sau ea poate determina un program de producție ideal pentru durata de viață a utilajelor.
Acest lucru ar trebui să fie reprodus în toate domeniile de activitate, de la determinarea timpilor de ciclu la livrarea produselor, până la eficiența energetică a instalației.
Pasul cinci: Evaluați, apoi reinvestiți
O mai mare vizibilitate a datelor poate oferi, de asemenea, organizațiilor o evaluare a costurilor, a beneficiilor și a rentabilității investițiilor (ROI) pentru schimbările pe care intenționează să le facă. Să ne imaginăm că un manager de producție speră să reducă timpii de schimbare a producției prin reprogramarea producției într-un mod mai optim. Cu ajutorul unui software inteligent pentru fabrici, rezultatele preconizate ale acestei schimbări pot fi generate automat, împreună cu informații despre modul în care aceasta ar putea avea un impact asupra restului locației.
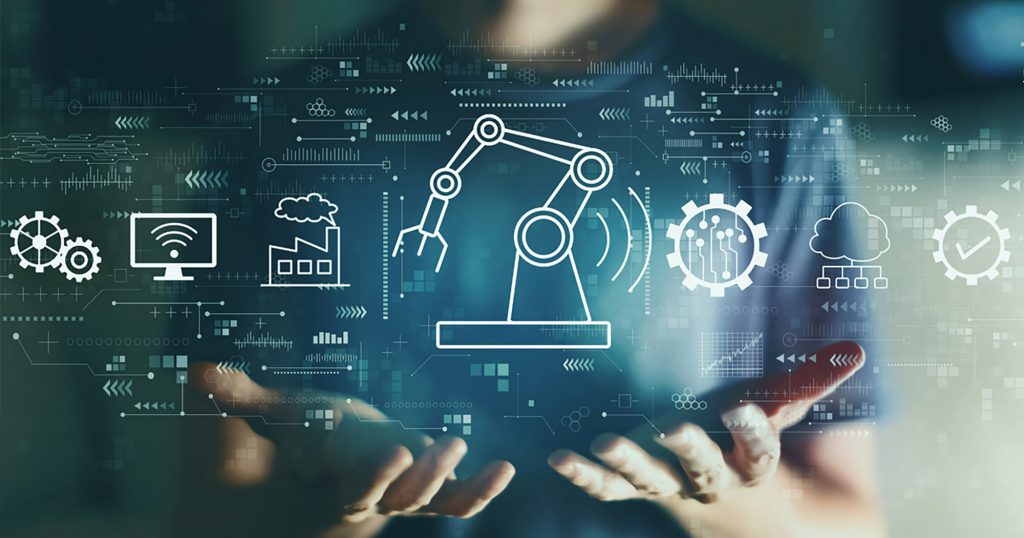
Mai mult, aceste date pot fi integrate cu alte domenii ale afacerii, cum ar fi sistemele informatice de întreprindere – planificarea resurselor întreprinderii (ERP). Să presupunem că modificările aduse programului de producție au ca rezultat materiale irosite – acest lucru ar putea fi posibil în domeniul alimentar, al băuturilor, al aplicațiilor farmaceutice sau în orice sector cu ingrediente care expiră. Prin integrarea datelor din alte domenii ale afacerii, consecințele acestei schimbări vor fi realizate din timp.
Pasul șase: Găsiți un software care să simplifice procesul
Cu cunoștințele dobândite în etapele anterioare, producătorii pot evalua modul în care pot atinge aceste obiective cu tehnologia lor existentă. De obicei, acest lucru este realizabil în întregime cu ajutorul unui software de control industrial, precum zenon de la COPA-DATA.
Cu toate acestea, aceasta este, de asemenea, etapa în care se analizează dacă sunt necesare alte tehnologii pentru a îndeplini aceste obiective. De exemplu, dacă o modificare a programului de producție menționat anterior nu este posibilă cu ajutorul muncii manuale, ar putea fi utilizată tehnologia robotică pentru a crește viteza de schimbare a produselor?
Six steps to the connected factory
STEFAN REUTHER, JANUARY 2021

KREATRON AUTOMATION SRL