Potrivit Consiliului Internaţional pentru Transport Curat (ICCT), vehiculele mai uşoare emit mai puţine emisii de CO2. Producătorilor de automobile le revine responsabilitatea de a produce componente mai eficiente din punct de vedere al greutăţii, dar, alături de metalele mai uşoare, cum ar fi aluminiul, oţelurile inoxidabile mai grele, fonta şi oţelul forjat rămân populare. A face ca aceste piese mai grele să fie eficiente din punct de vedere al greutăţii presupune prelucrarea lor la toleranţe mai stricte şi la modele mai complexe, dar acest lucru necesită o „abordare mai blândă”. Aici, Sangram Dash, Manager în aplicarea produselor pentru freze amovibile în cadrul Sandvik Coromant, explică modul în care freza CoroMill® MF80, mai uşoară şi cu aşchiere mai apropiată, sprijină o frezare de colţ şi o frezare frontală mai economice.
Conform raportului său „Fişă informativă”: Europa, Consiliul Internaţional pentru Transport Curat (ICCT) afirmă că: „Datorită corelaţiei directe dintre greutate şi masă, cu cât este mai greu un vehiculul, cu atât consumul de combustibil şi emisiile de CO2 sunt mai mari. Prin urmare, reducerea masei reprezintă o modalitate eficientă de a reduce emisiile unui vehicul.”
O modalitate de a obține acest lucru este „reducerea greutăţii”, care presupune construirea de maşini şi camioane mai puţin grele, ca o modalitate de a obţine o eficienţă a consumului de combustibil şi o manevrare sporite. Raportul McKinsey & Company intitulat Greutate redusă cu impact puternic estimează că „Măsurile de reducere a greutăţii pot contribui la reducerea emisiilor de CO2 într-o anumită măsură (o reducere de aproximativ 0,08 g de CO2 pe kilogram economisit).” Acesta continuă: „Dacă un producător de echipamente originale (OEM) reuşeşte să reducă greutatea vehiculului cu 100 kg, acesta economiseşte aproximativ 8,5 g de CO2 pe 100 km.”
Exemplul ilustrează modalitatea în care reducerea greutăţii poate aduce beneficii performanţei vehiculului. Totuşi, în timp ce producătorii de echipamente originale (OEM) adoptă materiale mai uşoare, cum ar fi aluminiul, pentru a obţine acest lucru, reducerea greutăţii nu presupune doar alegerea unui material care cântăreşte cel mai puţin. Materialele populare pentru piesele din industria construcţiilor de maşini, cum ar fi oţelurile forjate, aliajul de cobalt şi crom, Inconelul sau fonta cenuşie sau cea cu grafit nodular, sunt încă predominante — chiar dacă cântăresc mai mult decât aluminiul şi magneziul.
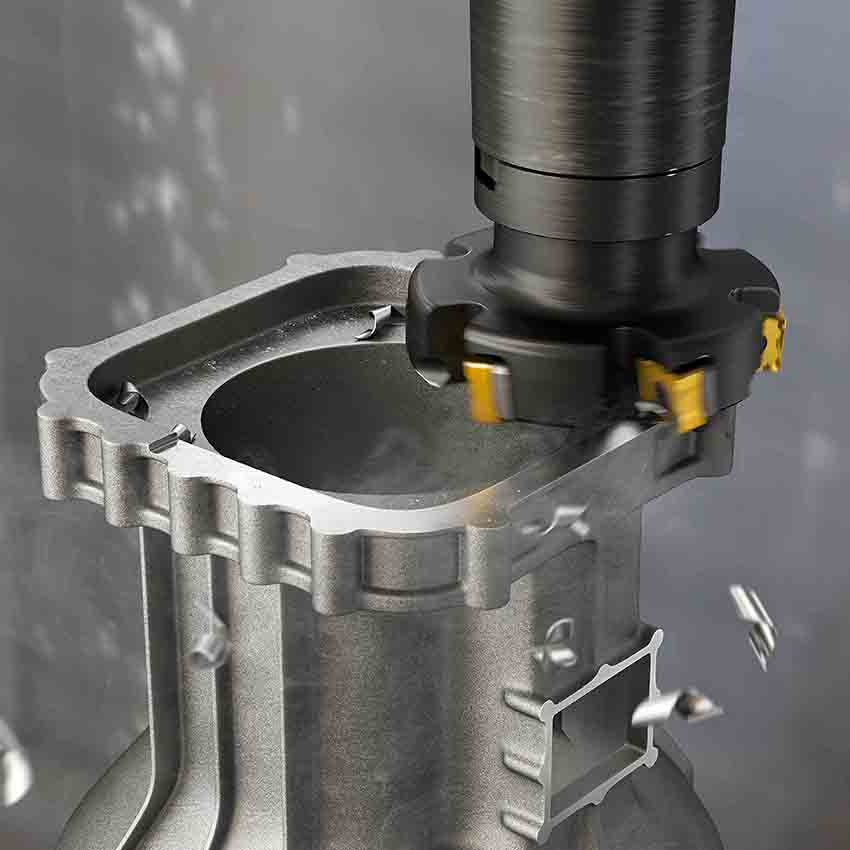
În schimb, producătorii trebuie să proiecteze profesional aceste metale „grele” ca fiind o alternativă mai eficientă din punct de vedere al greutăţii şi al rezistenţei faţă de metalele mai uşoare. Acest lucru înseamnă producerea de piese cu forme apropiate de cele finale pe baza unor modele mai complexe. În plus, multe dintre aceste modele necesită o acţiune de aşchiere mai uşoară pentru a minimiza impactul asupra sculei şi pentru a se asigura menţinerea formei componentei.
Provocarea producătorilor de echipamente originale (OEM) constă în producerea acestor componente mai complexe la cea mai înaltă calitate şi la un nivel de productivitate ridicat. Dar cum pot producătorii să obţină acest lucru, respectând în acelaşi timp reglementările privind emisiile şi menţinând un cost redus pe componentă? Răspunsul constă în soluţii de prelucrare mai fiabile, mai precise şi mai productive.
Unghiul corect
Producătorii de automobile trebuie să se străduiască să depăşească concurenţa atunci când prelucrează piese mai complexe, cu forme apropiate de cele finale, din materiale ISO-P dure. Obţinerea acestui lucru depinde de alegerea lor în ceea ce priveşte scula aşchietoare. De exemplu, sculele aşchietoare cu unghiuri de avans de 90 de grade generează forţe de aşchiere radiale şi, mai important, transferă mai multă putere de aşchiere departe de piesă. Acest lucru este ideal mai ales atunci când se prelucrează piese cu pereţi mai subţiri sau cu forme apropiate de cele finale.
Acest lucru ne aduce la subiectul frezării de colţ, o aplicaţie de frezare de bază, dar şi versatilă, care se recomandă atunci când este necesară producerea unei varietăţi de componente şi când trebuie îndepărtate rapid cantităţi mari de material de pe piesa de prelucrat. Datorită frezării de colţ, scula creează simultan o suprafaţă plană şi o suprafaţă de colţ, motiv pentru care se preferă un unghi de 90 de grade pentru piesa de prelucrat. Alte unghiuri pot fi şi sunt folosite în funcţie de aplicaţie, dar este esenţial să se folosească unghiul corect pentru a evita decalajele nedorite între freză şi piesa de prelucrat.
Pe piaţă există o serie de plăcuţe pentru sculele de frezare de colţ concepute pentru un unghi de frezare de aproape 90 de grade. În general, aceste plăcuţe sunt prevăzute cu opt muchii – patru în faţă şi patru în spate pentru a produce simultan suprafeţe de colţ şi suprafeţe plane – sau şase, în unele cazuri. Totuşi, specialiştii în prelucrare din cadrul Sandvik Coromant au simţit că există loc pentru un nou concept de frezare de colţ, care să aducă avantaje în ceea ce priveşte durabilitatea şi productivitatea sculei, precum şi avantaje economice pentru clienţi.
Rezultatul este freza CoroMill® MF80, concepută pentru aplicaţiile de frezare din industria construcţiilor de maşini, în materiale ISO-K şi ISO-P. Plăcuţele prezintă opt muchii aşchietoare, protecţie la aşchii şi micro-geometrie optimizată pentru siguranţă şi evacuare îmbunătăţită a aşchiilor, precum şi o muchie Wiper pentru o finisare superioară a suprafeţelor. Muchia aşchietoare este înclinată pentru a efectua acţiunea de aşchiere uniformă şi pentru a înregistra forţe de aşchiere reduse, ceea ce o face ideală pentru componente cu pereţi subţiri şi configuraţii de maşini cu stabilitate limitată. Bazat pe o platformă tehnologică similară cu cea a CoroMill® 345 existente, acest nou concept de frezare oferă un corp al frezei cu 40% mai uşor, dotat cu protecţie cu bailaguri şi un număr mare de plăcuţe pentru prelucrare sigură şi stabilă, chiar şi în aplicaţii cu lungime în consolă predispuse la vibraţii.
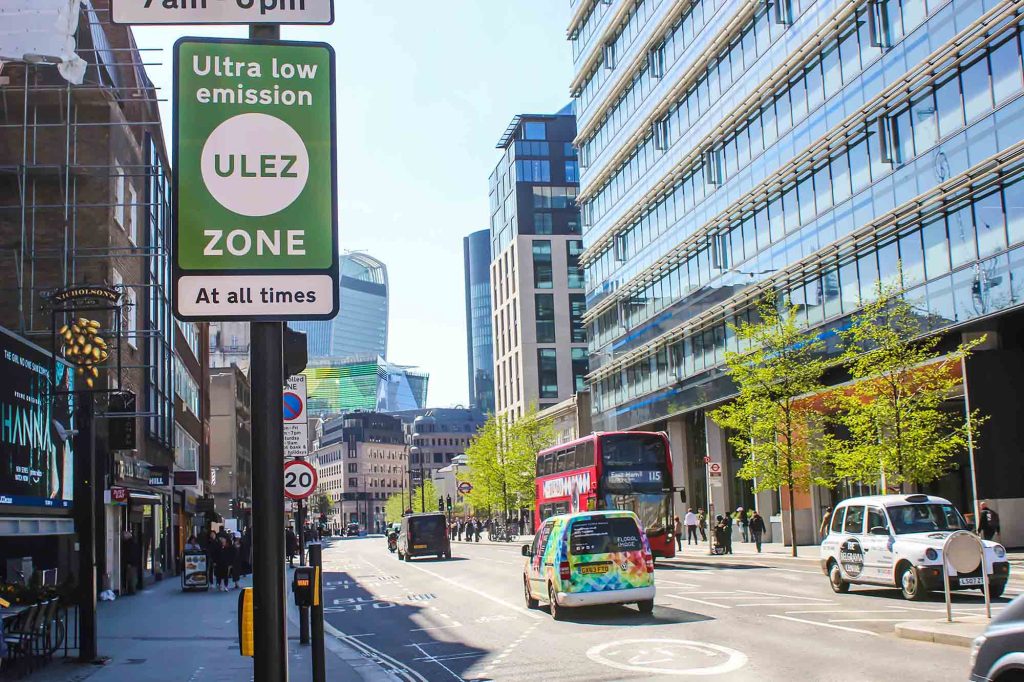
Unghiul de atac de 89,5 grade îi permite frezei cu muchie multiplă să lucreze în apropierea dispozitivului de prindere în timpul prelucrării. Unghiul de aproape 90 de grade a redus, de asemenea, forţele axiale, pentru o frezare îmbunătăţită a componentelor cu pereţi subţiri şi a dispozitivelor de prindere slabe, fără vibraţii şi trepidaţii. Acest lucru nu numai că îmbunătăţeşte precizia şi modul de utilizare a maşinii, dar asigură şi o durabilitate mai mare a sculei cu un debit de aşchii redus.
Testări de performanţă
Performanţa frezei CoroMill® MF80 a fost testată în comparaţie cu performanţa frezei concurenţei, la prelucrarea materialelor ISO-K şi ISO-P. Mai întâi, să analizăm testarea de performanţă a ISO-K, în care scula concurenţei şi freza CoroMill® MF80 au fost utilizate fiecare într-o aplicaţie de degroşare, pentru a produce suporturi dintr-o piesă de prelucrat din fier cu grafit nodular (SG) ISO-K (GJS400/K3.1.C.UT).
Ambele scule au funcţionat cu acelaşi regim de aşchiere – inclusiv cu o turaţie a pinolei (n) de 1000 de rotaţii pe minut (rot/min), o viteză de aşchiere (vc) de 250 de metri pe minut (m/min) şi o viteză de avans (vf) de 1200 de milimetri pe minut (mm/min). Fiecare freză a funcţionat cu o adâncime de aşchiere radială de 20-80 mm (ae) şi o adâncime de aşchiere axială de 2-3 mm (ap). A existat o uşoară diferenţă în ceea ce priveşte avansul pe dinte (fz), de 0,24 mm pentru freza concurenţei şi de 0,3 mm pentru freza CoroMill® MF80.
În final, freza concurenţei a produs zece componente în 55 de minute, înainte de a prezenta semne de uzură. Freza CoroMill® MF80, pe de altă parte, a funcţionat timp de 82 de minute şi a produs 15 componente în acest timp. Rezultatul înregistrat de client a fost o creştere a durabilităţii sculei cu 54% folosind freza Sandvik Coromant.